Building a conference table is a rewarding project that combines functionality with craftsmanship. Whether you’re creating a centerpiece for a corporate office or a collaborative space for a small team, the process allows you to design a custom piece that fits your specific needs. By using the right materials, tools, and methods, you can construct a durable and aesthetically pleasing table that enhances your workspace and fosters productivity.
This guide on how to build a conference table will walk you through the steps to build a professional-grade conference table, from planning to finishing.
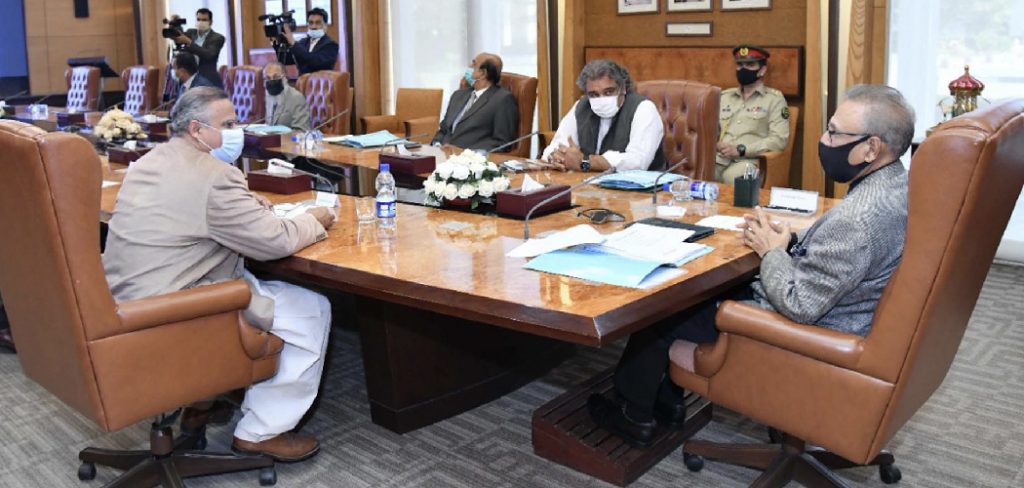
Why Build a Conference Table?
A conference table is more than just a surface to hold meetings. It serves as a focal point for discussions and decision-making, making it an essential piece of furniture in any workplace. Building a custom conference table allows you to tailor the design and size to meet your specific needs, whether it’s for a large boardroom or a small meeting space. It also gives you the opportunity to add unique features such as built-in power outlets and cable management systems, creating a functional and organized workspace.
Needed Materials
To build a conference table, you will need the following materials:
Wood
The type of wood you choose will greatly impact the appearance and durability of your conference table. Solid hardwoods like oak, maple, and cherry are popular choices for their strength and beautiful grain patterns. Alternatively, you can opt for engineered woods like plywood or medium-density fiberboard (MDF), which is a more affordable option.
Tools
Having the right tools is crucial to successfully building a conference table. Some essential tools include a circular saw or table saw, router, drill, clamps, and sanders. You may also need specialized woodworking tools like a biscuit joiner or pocket hole jig, depending on your chosen construction method.
Hardware
In addition to basic screws and nails, you will also need specific hardware such as drawer slides, hinges, and cable management systems. Be sure to choose high-quality hardware that is durable and can support the weight of your table.
8 Simple Step-by-step guidelines on how to build a conference table
Step 1: Plan and Design
The first step to building a conference table is to plan and design your table. Consider the size of your workspace, the number of people you need to accommodate, and any special features you want to incorporate. Create detailed drawings or use online software to visualize your design before moving on to the next step.
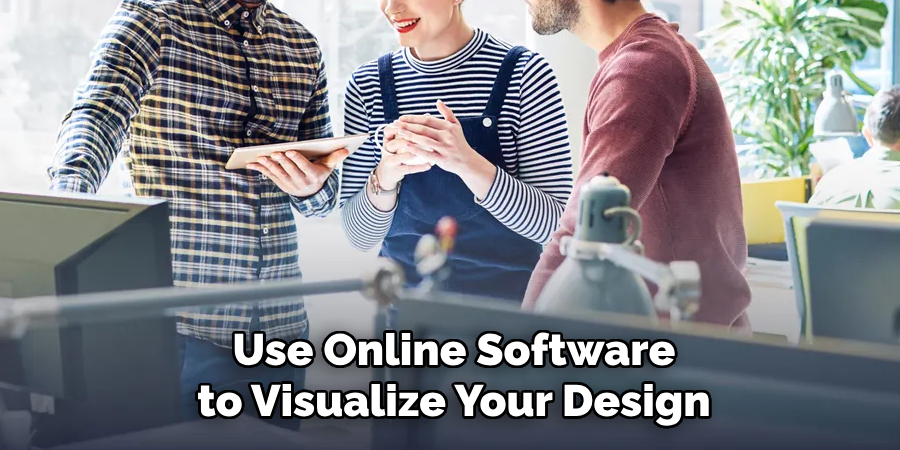
It is also important to consider the dimensions of your chosen materials and adjust your design accordingly. This will ensure you have accurate measurements for cutting and assembly.
Step 2: Prepare the Wood
If using solid wood, start by milling the lumber to the required sizes. If using engineered wood, cut it to size using a circular saw or table saw. Be sure to wear appropriate safety gear when handling power tools.
Next, sand all surfaces of the wood to remove any roughness or imperfections. This will provide a smooth finish and prevent any splinters.
Step 3: Join the Pieces
Once your wood pieces are prepared and sanded, it’s time to join them together to create the tabletop. Begin by aligning the pieces edge-to-edge according to your design. Use wood glue along the edges to bond the pieces securely. To ensure a strong and even connection, consider using dowels, biscuits, or pocket hole screws, depending on your preferred joinery method.
Clamp the pieces tightly together and leave them to dry for the recommended amount of time-based on the wood glue manufacturer’s instructions. Use a straight edge or level to check that the surface remains flat as it dries. Once the glue has set, remove the clamps and sand the joined surface to achieve a seamless, even finish before moving on to the next steps.
Step 4: Create the Base
While the tabletop dries, you can start building the base of your conference table. Depending on your design, this may involve cutting and joining wood pieces or using pre-made legs or frames.
If constructing your own base, be sure to carefully measure and cut the pieces according to your design plan. Use wood glue and screws for a strong connection.
Step 5: Attach the Base to the Tabletop
Once both the tabletop and base are complete, it’s time to attach them together. First, flip over the tabletop onto a flat surface with its bottom facing up. Place the base on top, aligning it with the corners of the tabletop. Use wood screws to secure the base to the underside of the tabletop, making sure it is centered and level.
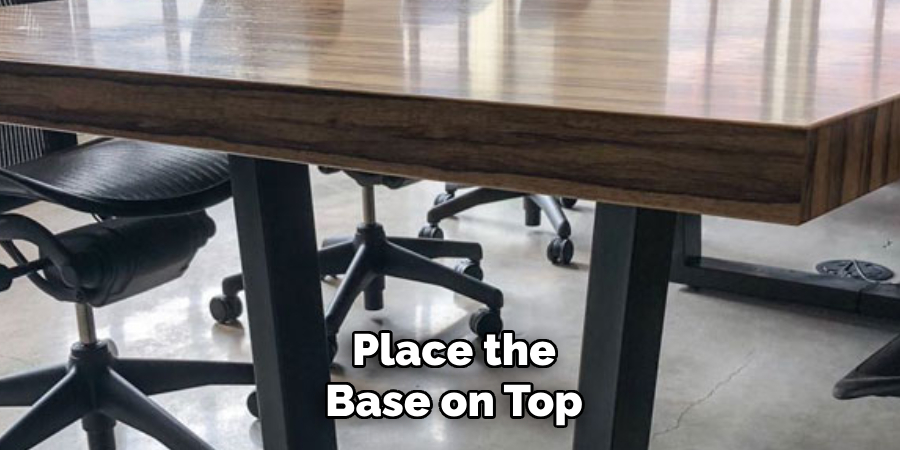
It may be helpful to have someone assist you during this step to ensure the base is aligned correctly.
Step 6: Add Finishing Touches
To enhance the appearance and durability of your conference room table design, consider adding finishing touches such as stain or paint. This will also allow you to match the table with existing furniture or décor in your workspace. Apply multiple coats for a smooth, professional finish.
You can also add any desired features at this stage, such as built-in power outlets or cable management systems.
Step 7: Optional Features
Depending on your specific needs and preferences, you may want to incorporate additional features into your conference table design. These may include drawers for storage, adjustable height mechanisms, or even wireless charging capabilities.
Before adding these features, make sure they are compatible with your chosen base and that you have the necessary tools and hardware for installation.
Step 8: Assemble and Enjoy
Once all the components are complete and dry, assemble the table by attaching any optional features and placing them in their designated space. Be sure to carefully read all assembly instructions to ensure proper installation and use.
Finally, enjoy your newly built conference table and the benefits of having a personalized, functional workspace for meetings and presentations.
Following these simple guidelines on how to build a conference table and using quality materials and tools, you can create a conference table that meets your specific needs and enhances the overall look and functionality of your workspace. Happy building!
Additional Tips
- Be precise with your measurements and cuts to ensure a professional finish.
- Use high-quality materials and hardware for long-lasting durability.
- Don’t forget to take breaks and stay safe by wearing appropriate gear when handling power tools.
- Consider having a designated workspace with ample lighting and ventilation for better construction results.
- Don’t be afraid to get creative and add personal touches to make your conference table unique. Remember, this is a piece of furniture that will be used frequently in your workspace, so make it functional and visually appealing.
- Lastly, have fun and enjoy the process of building something with your own hands! It’s a rewarding experience that can save you money and give you a sense of accomplishment. Happy building!
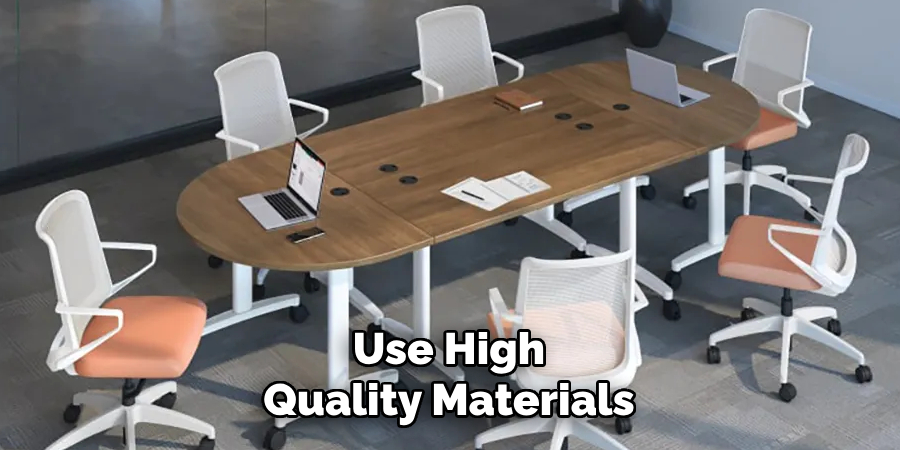
Frequently Asked Questions
Q1: Is It Necessary to Use Wood Glue When Joining the Tabletop Pieces?
A: Wood glue is highly recommended for a stronger and more secure bond. This will also help prevent any gaps or unevenness in the tabletop surface. The use of dowels, biscuits, or pocket hole screws can also help ensure a strong connection.
Q2: Can I Use Different Types of Wood for the Tabletop and Base?
A: Yes, you can mix and match different types of wood as long as they are compatible in terms of strength and weight. This can also create an interesting contrast in the appearance of your conference table.
Q3: How Long Should I Wait for the Wood Glue to Dry Before Removing Clamps?
A: The recommended drying time will depend on the type and brand of wood glue used. It is best to follow the instructions provided by the manufacturer for optimal results.
Q4: Do I Need to Sand the Tabletop After Applying Finishing?
A: Yes, sanding after finishing is recommended for a smooth and even surface. This will also help remove any excess finish or imperfections. Additionally, you can apply a topcoat for added protection and shine.
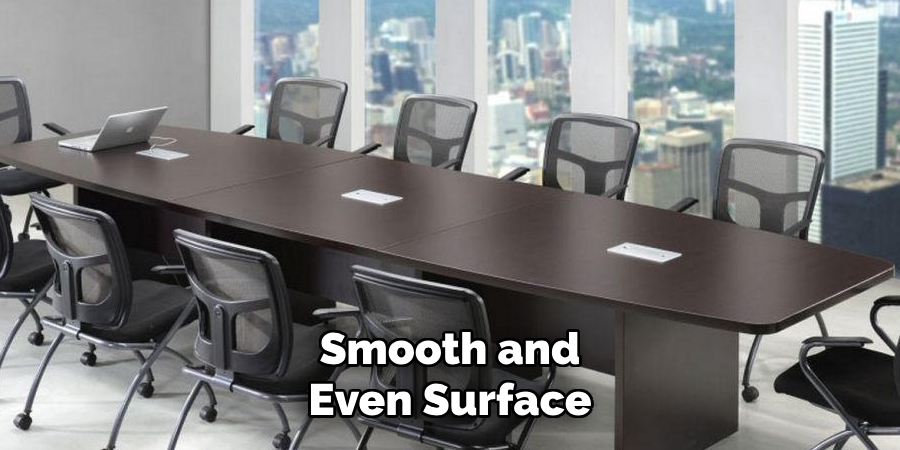
Q5: Can I Add Wheels to My Conference Table?
A: Yes, if your base design allows it, adding wheels or casters to your conference table can make it more versatile and easier to move around. Just make sure they are sturdy and have a locking mechanism for stability during meetings.
Conclusion
Building your own conference table is a rewarding and practical project that allows you to create a functional and personalized centerpiece for your workspace. By following the steps on how to build a conference table outlined in this guide and using high-quality materials, you can ensure your table is not only durable but also visually appealing.
Whether you’re hosting important meetings or brainstorming creative ideas, your custom-built conference table will contribute to a productive and professional environment. Remember, the key to success lies in careful planning, attention to detail, and a willingness to experiment with your design. Take pride in your craftsmanship and enjoy the benefits of a table tailored to your specific needs and style. Happy building!
Huston Douthit is a distinguished figure in the world of furniture design, with a decade of expertise creating innovative and sustainable furniture solutions. His professional focus lies in merging traditional craftsmanship with modern manufacturing techniques, fostering designs that are both practical and environmentally conscious. As the author of Fruniturix, Huston delves into the art and science of furniture-making, inspiring artisans and industry professionals alike.
Education
- RMIT University (Melbourne, Australia)
Associate Degree in Design (Furniture)- Focus on sustainable design, industry-driven projects, and practical craftsmanship.
- Gained hands-on experience with traditional and digital manufacturing tools, such as CAD and CNC software.
- Nottingham Trent University (United Kingdom)
Bachelor’s in Furniture and Product Design (Honors)- Specialized in product design with a focus on blending creativity with production techniques.
- Participated in industry projects, working with companies like John Lewis and Vitsoe to gain real-world insights.
Publications and Impact
In Fruniturix, Huston shares his insights on furniture design processes, materials, and strategies for efficient production. His writing bridges the gap between artisan knowledge and modern industry needs, making it a must-read for both budding designers and seasoned professionals.