Making a metal table can be a rewarding DIY project that combines creativity with practical skills. Whether you’re a seasoned welder or someone new to metalworking, crafting your own table allows you to customize its design, size, and functionality to meet your specific needs.
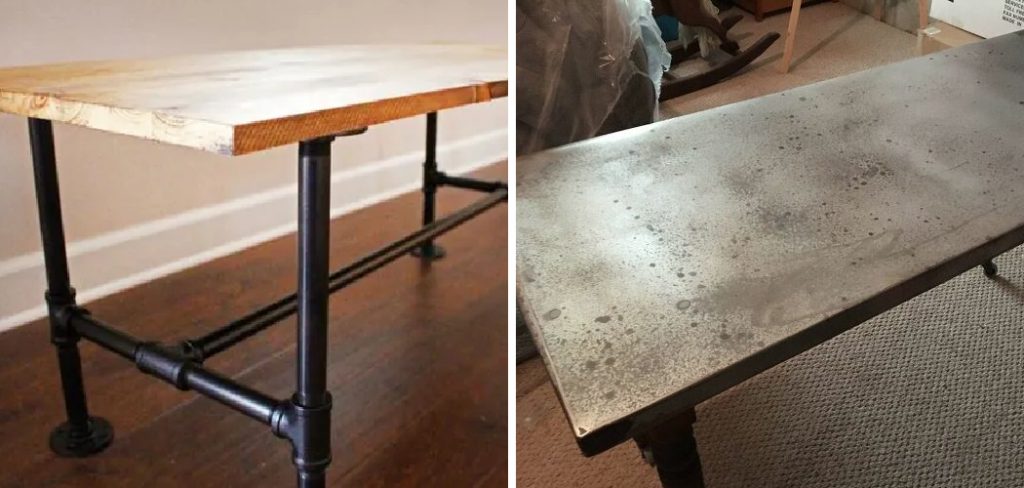
This guide on how to make a metal table will walk you through the essential steps, tools, and materials required to create a durable and stylish metal table, perfect for any space.
Why Make a Metal Table?
Before we dive into the nitty-gritty of creating a metal table, let’s first discuss why you should choose this material over others such as wood or plastic.
Durability:
Metal is an exceptionally durable material that can withstand heavy use and weight. A well-constructed metal table can last for decades without showing signs of wear and tear.
Versatility:
With metal, the possibilities are endless when it comes to design and style. You can create sleek and modern designs or go for a more rustic look by incorporating natural elements like wood.
Easy Maintenance:
Unlike wood, metal tables require minimal maintenance. They are easy to clean and do not need regular staining or refinishing.
Cost-Effective:
While metal may seem like an expensive material, it can be a cost-effective option in the long run. Since metal tables are durable and low-maintenance, you won’t have to replace or repair them frequently, saving you money in the long term.
Materials Needed
To make a metal table, you will need the following materials:
Metal Sheets or Bars:
Choose a metal that suits your design and budget, such as steel, aluminum, or copper. Make sure the metal is thick enough to support the weight of the table.
Welding Equipment:
To join metal pieces together, you will need a welding machine, protective gear (gloves, helmet), and welding rods suitable for your chosen metal.
Measuring Tape and Ruler:
Accurate measurements are crucial when making a table. Be sure to have both measuring tools on hand.
Saw:
You will need a saw to cut the metal sheets or bars to the desired size and shape.
Drill:
A drill will be necessary for creating holes in the metal for screws or bolts. Make sure to use a drill bit suitable for metal.
Clamps:
Clamps will come in handy when holding pieces of metal together during the welding process.
8 Step-by-step Guides on How to Make a Metal Table
Step 1: Design Your Table
Before you start working with the materials, it’s essential to have a clear design plan for your table. Begin by determining the purpose of the table—will it be a dining table, coffee table, or workbench? Decide the dimensions based on its intended use and the available space. Sketch out your design on paper or use design software to visualize the final product.
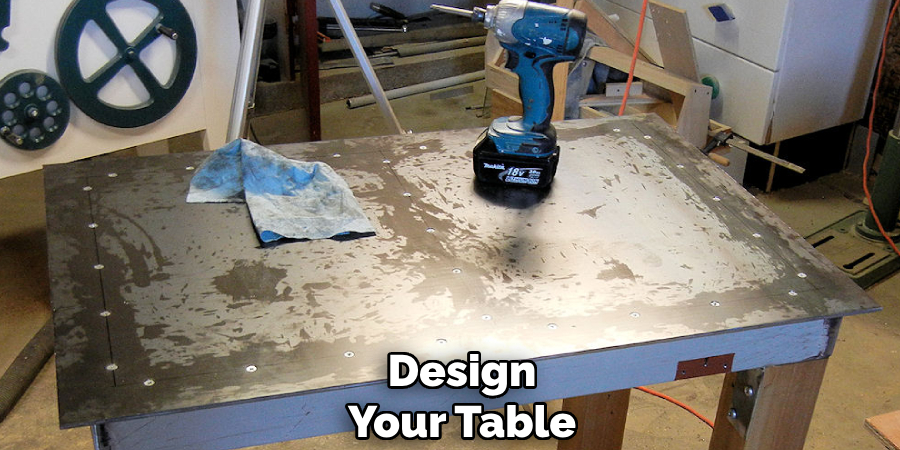
Consider additional elements like the shape of the legs and surface finish, as well as whether you want to incorporate other materials, such as a wooden top or glass inserts. A detailed design plan will not only guide you through the process but also ensure you have the right measurements and materials from the start.
Step 2: Cut the Metal Sheets or Bars
Once you have your design plan ready, the next step is to cut the metal sheets or bars to the required sizes and shapes as specified in your design. Start by marking the measurements on the metal using a measuring tape and a marker or scribe to ensure accuracy. Double-check your measurements before making any cuts to avoid mistakes.
Use a metal saw or an angle grinder with a cutting disc to make the cuts. Ensure that you are working in a well-ventilated area and wearing appropriate safety gear, including gloves, safety goggles, and a face mask, to protect yourself from metal shards and debris. Make clean, precise cuts to ensure the pieces fit together seamlessly during assembly. After cutting, use a file or a sanding tool to smooth the edges of the metal to prevent any sharp edges that could cause injuries or make assembly difficult.
Step 3: Weld the Pieces Together
With your metal pieces cut to size, it’s time to start welding them together. Begin by prepping the surfaces that will be welded by removing any rust or dirt with sandpaper or a wire brush. This step is crucial as clean surfaces ensure proper weld penetration and a stronger bond between the metal pieces.
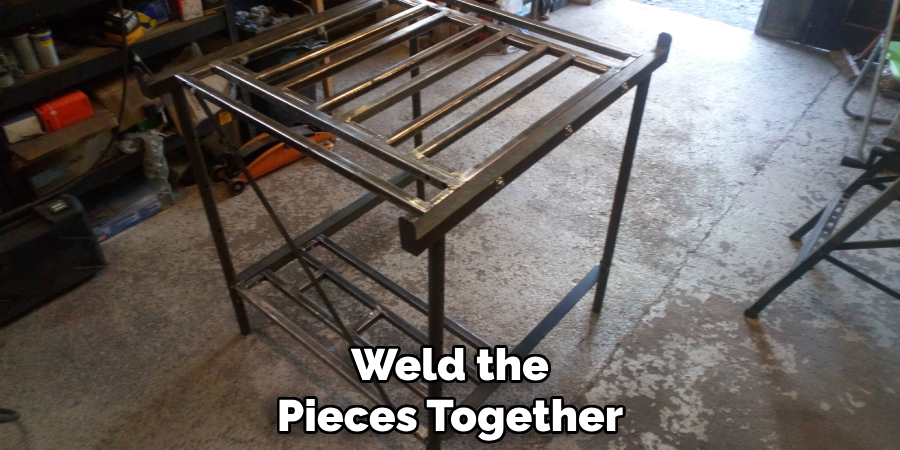
Next, clamp the pieces together in their desired positions before welding. This step helps to keep the parts in place and allows for better control during welding. Follow proper welding techniques, including selecting the appropriate welding rod, adjusting the heat settings on your machine, and maintaining a steady hand while moving along the seams. After each weld, check for any gaps or imperfections and fix them before moving on to the next joint.
Step 4: Add Legs and Supports
Once the main frame of the table is welded together, it’s time to add legs and supports. You can use metal bars or pipes for the legs or get creative by using unique materials like tree branches. Suppose you’re opting for wooden legs, pre-drill holes in both the metal frame and wood before attaching them with screws. Otherwise, weld the legs directly onto the frame.
To ensure stability, add crossbars or braces between each leg at a diagonal angle. These supports will also help distribute weight evenly across the table.
Step 5: Create a Tabletop
If you want to incorporate a wooden or glass tabletop, now is the time to create it. Measure and cut your chosen material according to your design plan and sand the edges for a smooth finish. Use clamps or brackets to securely attach the tabletop to the metal frame. If using glass, make sure it’s tempered for safety purposes.
The tabletop can also be made of metal, in which case you will need to weld the pieces together or create a seamless surface by using a grinder and filler material.
Step 6: Add Finishing Touches
Now that your table is assembled, it’s time to add some finishing touches. You can leave the metal frame as is for an industrial look or apply a coat of paint or powder coating for a sleeker finish. If using wood for the tabletop, stain or seal it according to your preference.
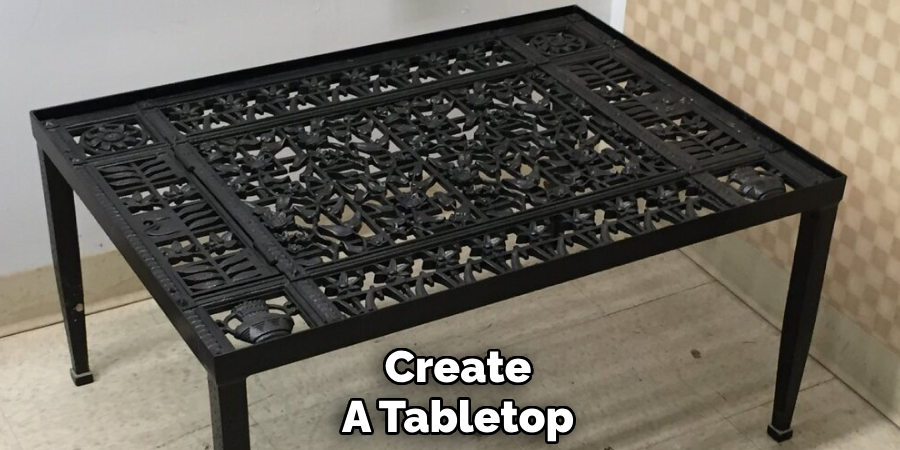
You may also choose to add decorative elements such as rivets, engravings, or patterns on the metal for a personalized touch. Be creative and have fun with this step!
Step 7: Test for Stability and Make Adjustments
Before using the table, make sure to test its stability by placing weight on various parts of the tabletop. If it wobbles or feels unsteady, make necessary adjustments such as adding additional supports or reinforcing weak spots with extra welds.
If the table is intended for outdoor use, ensure it’s weatherproof by applying a protective coating or choosing rust-resistant materials.
Step 8: Enjoy Your Custom Metal Table
Congratulations! You have successfully made your own metal table. Now it’s time to enjoy your creation and make some memories around it. With proper care and maintenance, your custom metal table will last for years to come. Use coasters for drinks, clean spills immediately, and periodically check for any signs of wear or damage.
Following these step-by-step guides on how to make a metal table will help you create a unique and sturdy metal table that fits your space and style. Remember to prioritize safety measures, take your time with each step, and have fun with the process. Happy welding!
Frequently Asked Questions
Q: Can I Use Any Type of Metal for My Table?
A: Yes, you can use a variety of metals like steel, aluminum, and copper. However, consider the strength and durability of each material when choosing the right one for your table.
Q: Do I Need Prior Welding Experience to Make a Metal Table?
A: It is recommended that you have some basic welding knowledge and skills before attempting to make a metal table. However, with proper research, guidance, and safety precautions, anyone can learn how to weld and make their own metal furniture.

Q: How Thick Should the Metal Sheets or Bars Be?
A: The thickness of the metal will depend on your design and intended use for the table. Thicker metals are generally stronger but also more challenging to cut and weld. Consult an expert or do thorough research before deciding on the appropriate thickness for your project.
Q: Can I Customize My Design As I Go?
A: Absolutely! Making a metal table is a creative and personal process, so feel free to make changes and add your own unique touches as you go. Just remember to prioritize stability and safety when making any modifications.
Conclusion
Making a custom metal table may seem like a daunting task, but by following these step-by-step guides and taking appropriate safety measures, you can create a unique piece of furniture that fits your style and space.
Experiment with different designs, materials, and finishes to create a one-of-a-kind metal table that will be both functional and visually appealing. Thanks for reading this article on how to make a metal table. A simple yet impactful metal desk makeover can transform your workspace, giving it a fresh, stylish, and functional appeal.
Huston Douthit is a distinguished figure in the world of furniture design, with a decade of expertise creating innovative and sustainable furniture solutions. His professional focus lies in merging traditional craftsmanship with modern manufacturing techniques, fostering designs that are both practical and environmentally conscious. As the author of Fruniturix, Huston delves into the art and science of furniture-making, inspiring artisans and industry professionals alike.
Education
- RMIT University (Melbourne, Australia)
Associate Degree in Design (Furniture)- Focus on sustainable design, industry-driven projects, and practical craftsmanship.
- Gained hands-on experience with traditional and digital manufacturing tools, such as CAD and CNC software.
- Nottingham Trent University (United Kingdom)
Bachelor’s in Furniture and Product Design (Honors)- Specialized in product design with a focus on blending creativity with production techniques.
- Participated in industry projects, working with companies like John Lewis and Vitsoe to gain real-world insights.
Publications and Impact
In Fruniturix, Huston shares his insights on furniture design processes, materials, and strategies for efficient production. His writing bridges the gap between artisan knowledge and modern industry needs, making it a must-read for both budding designers and seasoned professionals.