Creating a mini chair diy is a fun and creative DIY project that allows you to craft a small yet functional replica of a regular chair. Whether you’re building it as a decorative piece, a dollhouse accessory, or simply for practice in woodworking or crafting, the process can be both enjoyable and rewarding.
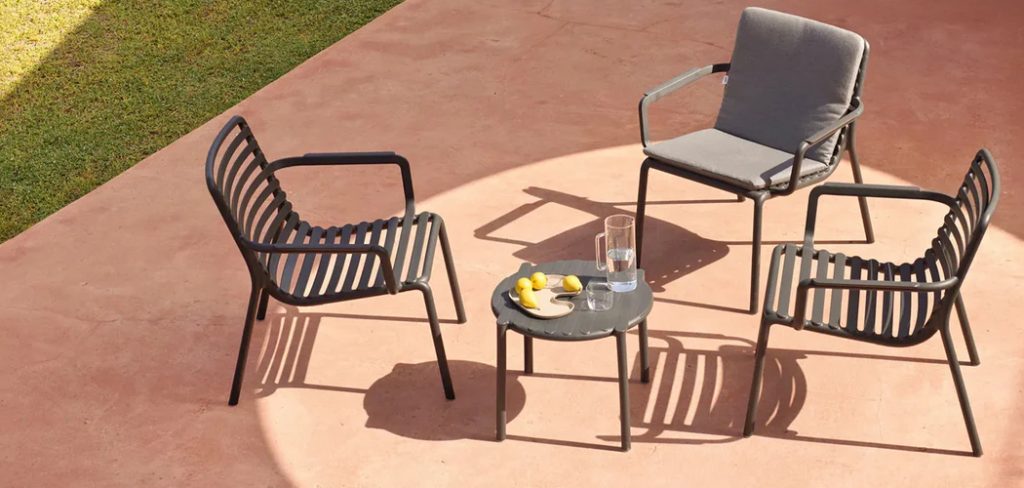
In this blog post we will show you how to make a mini chair so that it functions properly. Read on to learn more about which components and tools are needed for the job as well as detailed instructions on completing the task!
What is a Mini Chair and Its Uses?
A mini chair is a scaled-down version of a full-sized chair, meticulously crafted to replicate its larger counterpart in both form and function. These miniature creations often serve as decorative pieces or are used in dollhouses, model displays, or artistic exhibits. They can also be utilized as unique gifts or as practical tools to practice craftsmanship and woodworking techniques.
Beyond aesthetics, mini chairs are popular in educational settings, aiding in teaching design principles or engineering concepts. Their versatility and charm make them appealing for both creative hobbyists and practical applications alike.
Materials and Tools Needed
To create a mini chair, you will need a selection of materials and tools to ensure precision and durability. Common materials include wood, plastic, or metal, depending on the desired style and purpose. For wooden mini chairs, materials like balsa wood or plywood are typically used due to their lightweight and easy-to-work-with nature. Essential tools for crafting include a ruler or measuring tape for accuracy, a saw for cutting pieces to size, sandpaper for smoothing edges, and glue or nails for assembly. Additional tools like clamps, paint, and decorative elements may also be used to enhance the final design. Ensuring you have the right materials and tools on hand will make the crafting process both efficient and enjoyable.
10 Methods How to Make a Mini Chair
1. Decide on the Purpose and Scale of the Mini Chair
Before gathering materials or making any cuts, the first and most crucial step is to determine the intended use and scale of your mini chair.
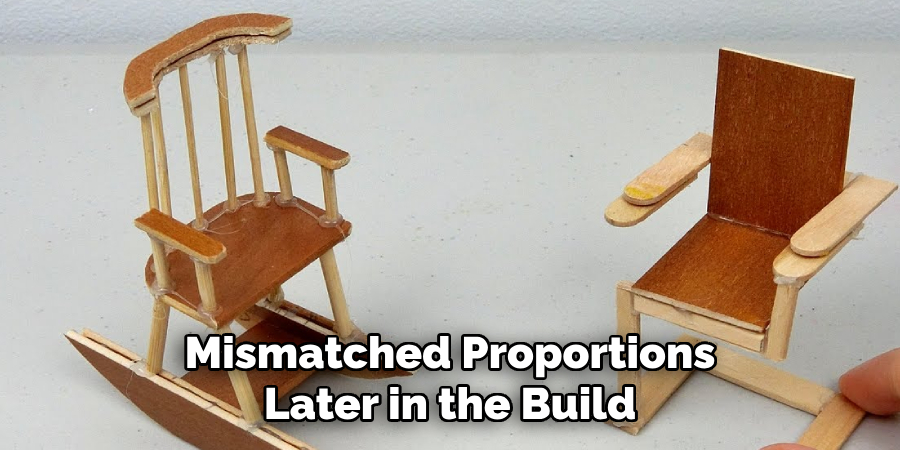
Will it be part of a dollhouse, a decorative tabletop piece, or a functional chair for a small toy? The purpose will dictate not only the dimensions but also the type of materials you’ll use. Miniature chairs for 1:12 scale dollhouses, for instance, are significantly smaller than display chairs meant for shelves. Clarifying the size and purpose helps you plan accurately and avoid mismatched proportions later in the build.
2. Choose the Right Materials for Authenticity and Strength
The materials you select will affect the look, durability, and ease of assembly. Wood is the most common choice for miniature chairs because it mimics real furniture on a small scale and is relatively easy to shape and glue. Balsa wood, craft sticks, dowels, or even scraps from larger woodworking projects are excellent options. For a more rustic or whimsical look, twigs or branches can also be used.
If you prefer an upcycled approach, cardboard, popsicle sticks, or even metal wire can be incorporated. Pick materials that are easy to cut and strong enough to hold their shape at a small scale.
3. Sketch a Simple Chair Design with Measured Dimensions
Once you’ve selected your scale and materials, take time to draw a detailed sketch of your mini chair. Include measurements for each component: legs, seat, backrest, and supports. Even a basic chair needs structure and balance, so plan carefully where each part will connect.
Consider whether you want a simple stool-style chair or one with arms and a backrest. Your sketch should act as your blueprint throughout the build, guiding each cut and ensuring consistency. Accuracy at this stage makes the entire process smoother and the final piece more polished.
4. Cut Out All Chair Parts with Precision
Using your measured plans, carefully cut each piece of the chair using a small hobby knife, razor saw, or fine-toothed handsaw, depending on the material. Precision is key—slight irregularities at a miniature scale can throw off the entire balance. Cut the four legs to equal length, the seat as a square or rectangle, and the backrest to your desired height.
For added detail or strength, you can also cut small rails or cross-braces. Smooth out all edges with fine-grit sandpaper to remove splinters and prepare the pieces for gluing.
5. Assemble the Base Frame Starting with the Legs and Seat
Begin the assembly by attaching the legs to the underside of the seat. It’s easiest to glue two opposing legs first, then add the remaining two once the first pair is stable. Use wood glue or strong craft adhesive and hold the pieces in place with clamps, tweezers, or masking tape while they set.
Make sure the legs are perpendicular and evenly spaced—check with a miniature square or ruler if necessary. Once the base is secure and dry, you have the core structure of your mini chair and can move on to building it upward.
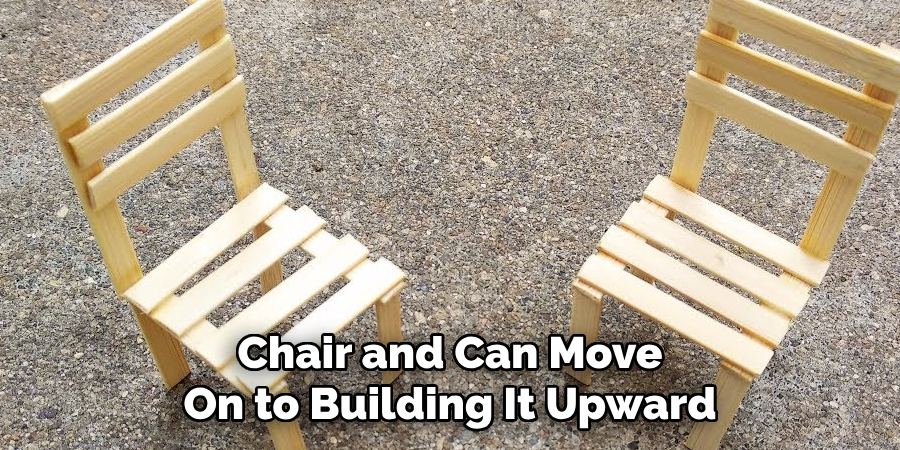
6. Add the Backrest for Comfort and Realism
Once the base is stable, attach the backrest to the rear edge of the seat. If your design includes vertical supports or slats, glue these in place first before adding the top rail of the backrest.
For a sturdier hold, cut small notches into the seat or legs where the backrest will fit. You can also reinforce the connection with corner braces or a dab of hot glue. Make sure the backrest is centered and aligned vertically so it doesn’t lean awkwardly. This step brings personality and realism to the mini chair’s overall form.
7. Add Decorative Details and Finishing Touches
Now that the chair’s structure is complete, you can enhance its charm with decorative elements. Consider adding carved or cut-out shapes in the backrest, armrests if your design allows, or crossbars between the legs for extra authenticity.
You can also embellish the seat with a tiny cushion, made from fabric and a bit of stuffing, for a cozy touch. Add wood beads for chair feet or finials to give your mini chair character. These small details make your piece feel more lifelike and unique.
8. Paint or Stain the Chair for a Finished Look
Finishing your chair with paint or stain brings the design to life. Choose a paint color that complements its setting—a classic white for a farmhouse feel, a bright hue for modern flair, or a wood stain for a timeless touch. Apply the finish with a small brush or sponge applicator, taking care not to overload it and obscure the chair’s details.
Allow each coat to dry completely before applying the next. If you stained the chair, consider sealing it with a clear miniature-safe varnish for added durability and a subtle shine.
9. Let Everything Dry and Set Before Handling
Patience is essential in miniature furniture making. Once your chair is painted or stained, allow all adhesives and finishes to cure fully. Drying times can vary depending on the glue or paint used, so refer to product instructions. Rushing this step can result in misaligned parts, smudges, or even collapsed joints.
Once dry, check for any loose areas or uneven finishes and touch up where needed. A fully cured mini chair will be much easier to handle and will last longer without risk of damage.
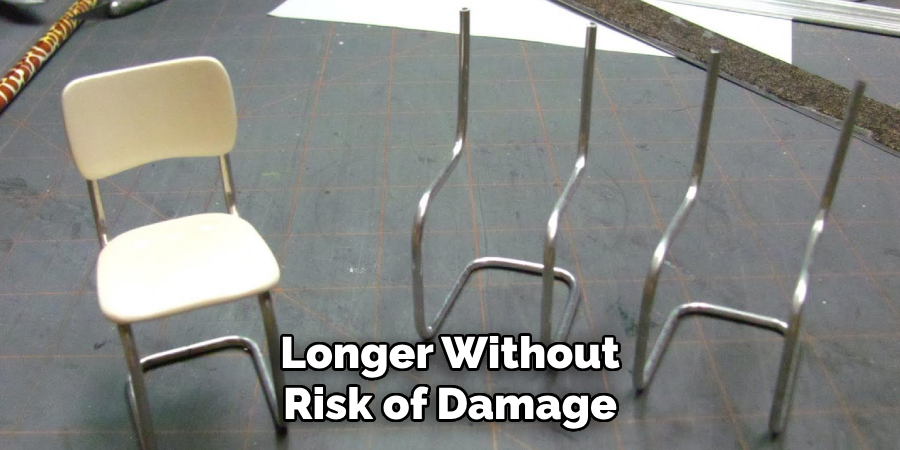
10. Display or Use Your Mini Chair with Pride
Your mini chair is now ready to be displayed or used in its tiny environment. Whether it becomes part of a dollhouse living room, sits on a bookshelf as decoration, or holds a small potted plant, your handcrafted chair adds personality and creativity to any space. If you’re crafting multiple chairs, use your first one as a template for consistency.
And if gifting it, consider packaging it in a small custom box or pairing it with a matching miniature table. Making a mini chair is a blend of art, craft, and precision—and now you have a delightful piece to show for your effort.
Maintenance and Upkeep
To ensure your handcrafted miniature chair remains in excellent condition, proper care is essential. Regularly dust it with a soft brush or cloth to keep it free from dirt and debris. If the chair is made of wood, a light application of furniture polish can help maintain its sheen, but make sure to use a polish suitable for small, delicate items.
For chairs painted or varnished, avoid exposing them to excessive moisture or direct sunlight, as this can cause discoloration or damage to the finish. If the chair includes fabric components, gently spot clean them as needed with a mild cleaner and allow them to air dry completely. By taking these steps, your mini chair will retain its charm and quality for years to come.
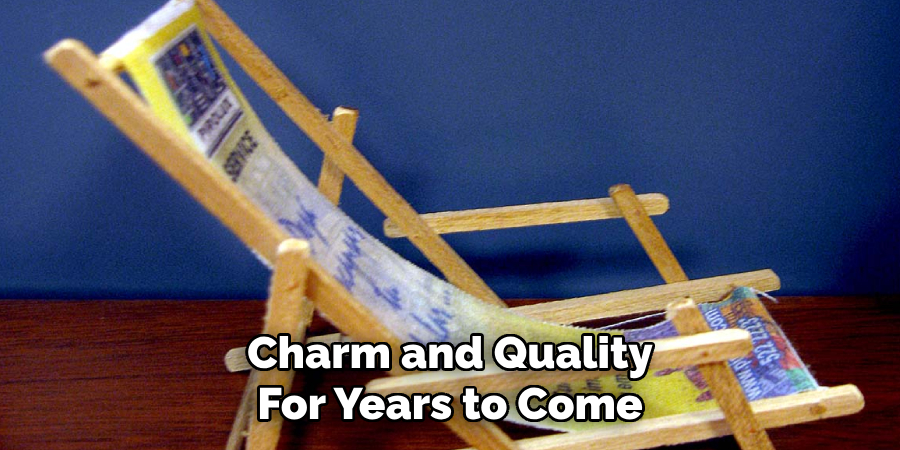
Conclusion
Creating a mini chair is a deeply satisfying project that blends creativity with fine craftsmanship. These ten detailed methods guide you through every stage, from initial concept to final finish, ensuring that your miniature furniture is not only adorable but also structurally sound. Thanks for reading our blog post on how to make a mini chair! We hope you found it helpful and informative.
Huston Douthit is a distinguished figure in the world of furniture design, with a decade of expertise creating innovative and sustainable furniture solutions. His professional focus lies in merging traditional craftsmanship with modern manufacturing techniques, fostering designs that are both practical and environmentally conscious. As the author of Fruniturix, Huston delves into the art and science of furniture-making, inspiring artisans and industry professionals alike.
Education
- RMIT University (Melbourne, Australia)
Associate Degree in Design (Furniture)- Focus on sustainable design, industry-driven projects, and practical craftsmanship.
- Gained hands-on experience with traditional and digital manufacturing tools, such as CAD and CNC software.
- Nottingham Trent University (United Kingdom)
Bachelor’s in Furniture and Product Design (Honors)- Specialized in product design with a focus on blending creativity with production techniques.
- Participated in industry projects, working with companies like John Lewis and Vitsoe to gain real-world insights.
Publications and Impact
In Fruniturix, Huston shares his insights on furniture design processes, materials, and strategies for efficient production. His writing bridges the gap between artisan knowledge and modern industry needs, making it a must-read for both budding designers and seasoned professionals.