Rattan furniture has long been celebrated for its unique combination of lightweight construction, durability, and timeless style. Among its many forms, rattan chairs stand out as versatile pieces that can complement a variety of interior or outdoor settings.
Their popularity stems from several factors, including their eco-friendly nature, aesthetic appeal, and adaptability to different design styles, from rustic to modern. Crafted from sustainable materials, rattan chairs bring a natural charm to any space and offer functionality and endurance when properly maintained.
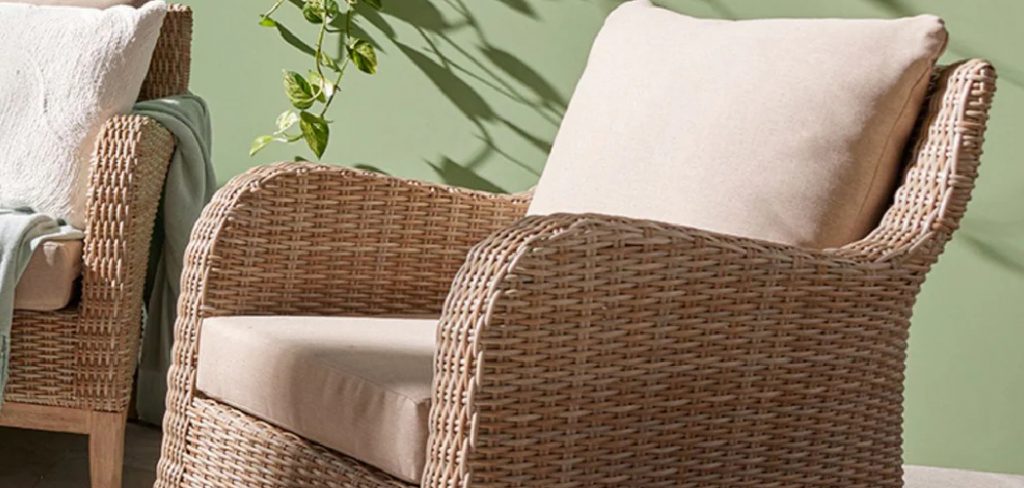
This article aims to serve as a comprehensive guide on how to make a rattan chair. Whether you are an enthusiast looking to explore a new skill or simply curious about the craftsmanship behind these elegant pieces, this step-by-step guide will walk you through the entire process—from selecting materials and constructing the frame to weaving and applying the perfect finishing touches.
Understanding Rattan and Its Properties
What is Rattan?
Rattan is a vine-like plant that grows abundantly in tropical regions, particularly in Southeast Asia. Known for its long, slender, and flexible stems, rattan is harvested for furniture manufacturing, home decor, and various crafts. Its natural aesthetic and strength make it popular, especially for chairs and outdoor furnishings.
Natural vs. Synthetic Rattan: Pros and Cons
Natural rattan is highly valued for its authenticity and organic look, which blends seamlessly with nature-inspired or rustic designs. It is also biodegradable and eco-friendly. However, it can be vulnerable to weather damage if not properly treated, especially in humid or wet environments. On the other hand, synthetic rattan—made from polyethylene or resin—is resistant to UV light, moisture, and mildew, making it an ideal option for outdoor furniture. While synthetic rattan lacks the authentic charm of its natural counterpart, it excels in durability and maintenance.
Differences Between Rattan, Bamboo, and Wicker
Rattan is often confused with bamboo and wicker, but they differ significantly. Bamboo is a hollow grass that is rigid and less flexible than rattan. Wicker, by contrast, is not a material; it refers to the weaving technique used to create furniture from materials like rattan, cane, or synthetic fibers.
Why Rattan is Ideal for Chair Making
Rattan’s flexibility allows it to be molded into various shapes, while its inherent strength ensures it can support significant weight. Additionally, its weather resistance and adaptability make it suitable for both indoor and outdoor applications. When appropriately treated, rattan can withstand years of use without losing its charm or structure.
Preparing Rattan for Crafting
Before crafting begins, rattan must be soaked in water to enhance its pliability. This process softens the fibers, allowing them to be easily bent and shaped without cracking or breaking.
After shaping, the material is left to dry and is often treated with a protective coating to increase durability and prevent damage from moisture, pests, or UV exposure. Proper preparation is essential to ensure the final product is both durable and aesthetically pleasing.
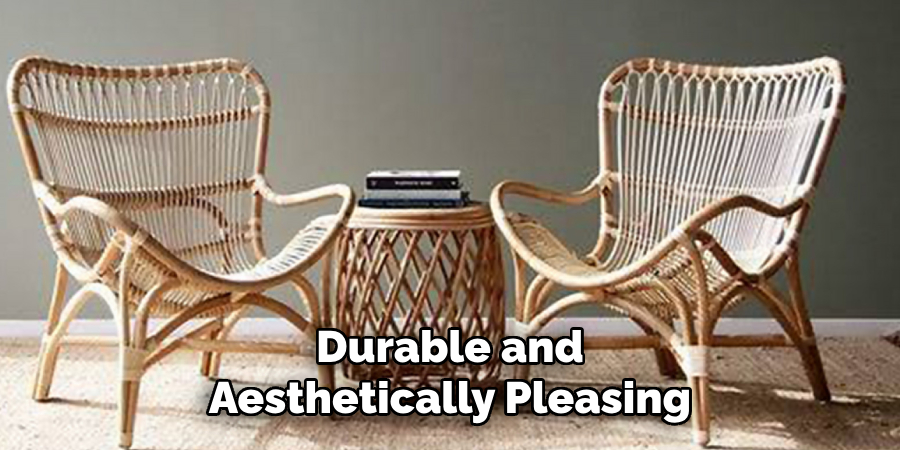
Gathering Materials and Tools
Essential Materials
To begin crafting a diy rattan chair, you must gather specific materials that ensure functionality and aesthetic appeal. The most important components include rattan poles for the framework and rattan cane strips for weaving intricate patterns. Depending on your design, a wooden frame can be incorporated to provide additional structure and stability.
Necessary Tools
Having the right tools is crucial for efficient and successful crafting. Essential tools include a hand saw for cutting rattan poles to the desired size, sandpaper to smooth rough edges, and a measuring tape to ensure precision. Wood glue is also vital for securing joints and enhancing the overall strength of the chair. Steam or hot water is also required to soften the rattan, making it pliable for shaping and weaving.
Choosing the Right Type of Rattan for Your Chair
Selecting the appropriate type of rattan is a key step in the process. Different parts of the chair, such as the frame, seat, and backrest, may require varying levels of thickness and flexibility.
Thicker, sturdier rattan poles are ideal for the framework, providing strong support, whereas thinner, more flexible cane strips are perfect for weaving detailed patterns. Careful selection will ensure the chair is both durable and visually appealing.
How to Make a Rattan Chair: Building the Chair Frame
Designing Your Chair
Before starting the construction, it is essential to design the chair and decide on its style and dimensions. Sketch a detailed plan that includes measurements for each part of the chair, such as the legs, backrest, seat, and armrests (if applicable). Common rattan chair styles include armchairs, lounge chairs, and dining chairs.
Each style has unique characteristics, so choose one that fits your aesthetic preference and intended use. A well-prepared sketch serves as a blueprint, ensuring accuracy and minimizing errors during the building process.
Constructing the Frame
Once the design is complete, cut the rattan poles to the appropriate sizes based on your sketch. Use a measuring tape for precision and a hand saw for clean cuts. Typically, thicker rattan poles are used for the chair’s legs, backrest, and seat frame to provide sturdy support. Join the pieces together using wood glue to attach the connecting poles securely. For additional stability, incorporate rattan bindings or rope around the joints, ensuring the frame can withstand weight and usage over time.
Reinforcing the Frame
To further enhance the frame’s strength, apply wood glue generously at all key connection points. If necessary, add small wooden or rattan supports to reinforce areas such as the corners of the seat or the joint sections of the backrest and legs. This will create a solid foundation, ensuring the chair maintains its durability and shape for long-term use. Proper reinforcement is crucial, especially if you plan to add intricate weaving to the seat and backrest later.
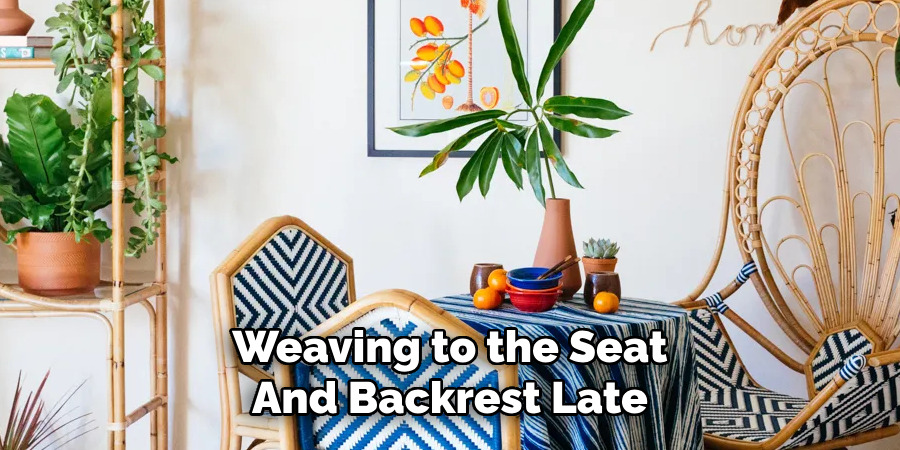
Weaving the Seat and Backrest
Basic Weaving Techniques
Weaving the seat and backrest is essential to creating a beautiful and functional chair. The over-under weaving method is a classic technique for achieving a clean and timeless look.
Another popular approach is the herringbone pattern, which adds depth and texture to the design. The basketweave pattern provides a sophisticated variation for those seeking a more intricate style. Experimenting with these techniques can enhance the chair’s aesthetic and align it with your taste.
Step-by-Step Seat Weaving
Begin the weaving process by securely attaching the rattan cane to the frame. Start at one side of the seat frame, tying or securing the cane with strong knots or staples depending on the structure. Use even spacing during this initial phase to ensure the weave will be tight and consistent. Proceed with the selected weaving method, keeping tension on the cane consistent to avoid sagging or gaps.
For a uniform finish, periodically adjust and tighten the weave where necessary, maintaining even spacing throughout. Once the weave is complete, secure the ends firmly and trim any excess material for a tidy finish.
Backrest Weaving Options
For the backrest, consider designs that prioritize both comfort and aesthetics. Using wider rattan strips can enhance comfort, providing a smoother surface to lean against. Decorative patterns such as lattice or diagonal weaves can add visual interest and make the backrest a unique focal point.
Start weaving from the bottom of the backrest frame, carefully securing the strips in place to prevent shifting. Experiment with layering techniques or combining patterns for a custom design. With attention to detail and creativity, the woven seat and backrest will provide comfort and elevate the overall craftsmanship of the chair.
Finishing Touches and Polishing
Trimming and Sanding
After completing the weaving, carefully inspect the chair for any rough edges or protruding material. Use a sharp blade or scissors to trim excess rattan or cane material, ensuring a clean and polished look. Next, sand down any rough surfaces, focusing on the edges of the frame and the woven areas.
Fine-grit sandpaper works best for smoothing and refining the surface without causing damage. This step enhances the chair’s aesthetic appeal and makes it safer and more comfortable to use by removing splinters or sharp edges.
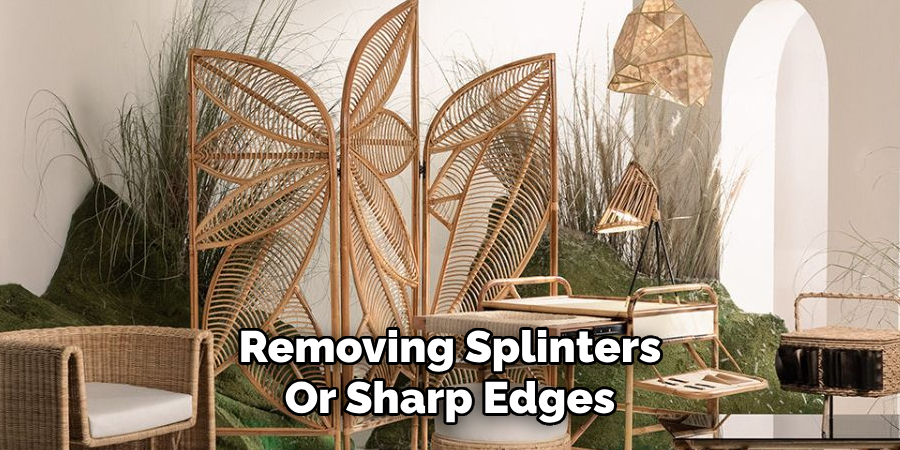
Sealing and Protecting the Chair
To enhance the chair’s durability, apply a protective finish such as varnish or clear lacquer. This coating helps shield the material from moisture, wear, and discoloration over time, extending the life of your chair.
Use a brush or spray applicator for a smooth and even finish, following the manufacturer’s instructions for best results. Allow the sealant to fully dry before handling the chair to ensure proper adhesion and protection.
Optional Customization
Consider adding cushions or upholstering the seat and backrest for additional style or comfort. Cushions can be selected in a variety of colors and patterns to match your décor. Alternatively, staining the rattan in a darker or lighter shade offers a personalized touch while complementing your interior design. These finishing touches allow you to adapt the chair to fit your specific aesthetic and practical needs.
Common Mistakes to Avoid
When working with rattan furniture, several common mistakes can compromise the quality and longevity of the final product.
Using Dry Rattan Without Soaking
One major error is attempting to weave or shape dry rattan. When rattan is not properly soaked beforehand, it becomes brittle, leading to cracks and breakage during crafting. Always ensure rattan has been soaked in water for adequate pliability, allowing easier manipulation and preventing unnecessary damage.
Weak Joints and Poor Weaving
Another frequent mistake is neglecting to reinforce weak joints or failing to ensure a tight, uniform weave. Loose weaves or weak areas in the structure can decrease the overall stability of the chair, making it prone to wobbling or collapsing over time. Regularly inspect and reinforce any problem areas to ensure a durable final product.
Skipping Protective Finishes
Failing to apply a proper sealing finish significantly shortens the chair’s lifespan. Protective coatings, like varnish or lacquer, shield rattan from moisture and wear, preventing rotting, discoloration, and splintering. Skipping this vital step leaves the chair vulnerable to the elements, undermining its durability and long-term value.

Maintenance and Care Tips
Cleaning and Dusting Regularly
To keep your rattan chair looking its best, clean it regularly using a damp cloth and mild soap. Gently wipe the surface to remove dirt and dust, ensuring you reach all the nooks and crannies. Avoid using abrasive cleaners, as they can damage the delicate rattan fibers.
Avoiding Excessive Moisture
Rattan furniture should be protected from excessive moisture to prevent weakening or rotting. Avoid exposing it to high humidity or direct rain, as water can seep into the material, causing damage over time. Always position your chair in a dry, well-ventilated area, and consider using protective covers outdoors.
Repairing Damaged Weaving
If you notice broken or loose strands in the weaving, act promptly to repair them. Replace broken strands by carefully weaving in new ones, matching the original pattern. Wood glue can help secure the new strands firmly in place, restoring functionality and aesthetics.
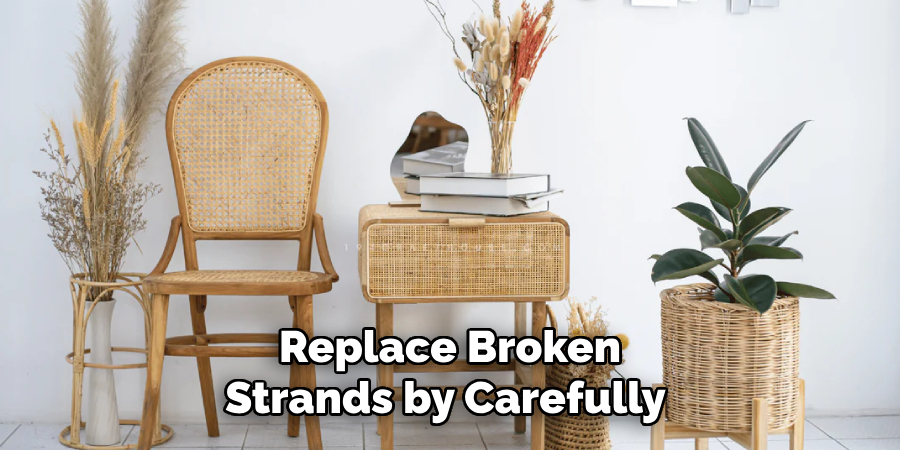
Conclusion
Creating rattan furniture is a rewarding process that involves thoughtful material selection, precise frame construction, careful weaving, and attention to finishing details. By understanding the steps on how to make a rattan chair, you can craft a unique piece that combines functionality with beauty.
Don’t hesitate to experiment with designs and patterns to reflect your style, making each chair unique. Handmade rattan furniture, when well-crafted, remains durable and timeless, offering years of use and charm. Your rattan chair can become a lasting centerpiece in your home or outdoor space with care and creativity.
Huston Douthit is a distinguished figure in the world of furniture design, with a decade of expertise creating innovative and sustainable furniture solutions. His professional focus lies in merging traditional craftsmanship with modern manufacturing techniques, fostering designs that are both practical and environmentally conscious. As the author of Fruniturix, Huston delves into the art and science of furniture-making, inspiring artisans and industry professionals alike.
Education
- RMIT University (Melbourne, Australia)
Associate Degree in Design (Furniture)- Focus on sustainable design, industry-driven projects, and practical craftsmanship.
- Gained hands-on experience with traditional and digital manufacturing tools, such as CAD and CNC software.
- Nottingham Trent University (United Kingdom)
Bachelor’s in Furniture and Product Design (Honors)- Specialized in product design with a focus on blending creativity with production techniques.
- Participated in industry projects, working with companies like John Lewis and Vitsoe to gain real-world insights.
Publications and Impact
In Fruniturix, Huston shares his insights on furniture design processes, materials, and strategies for efficient production. His writing bridges the gap between artisan knowledge and modern industry needs, making it a must-read for both budding designers and seasoned professionals.