Are you looking for a simple and stylish way to add storage space to your home? Look no further than wall shelves! These versatile pieces of furniture not only provide storage but also serve as decorative accents in any room.
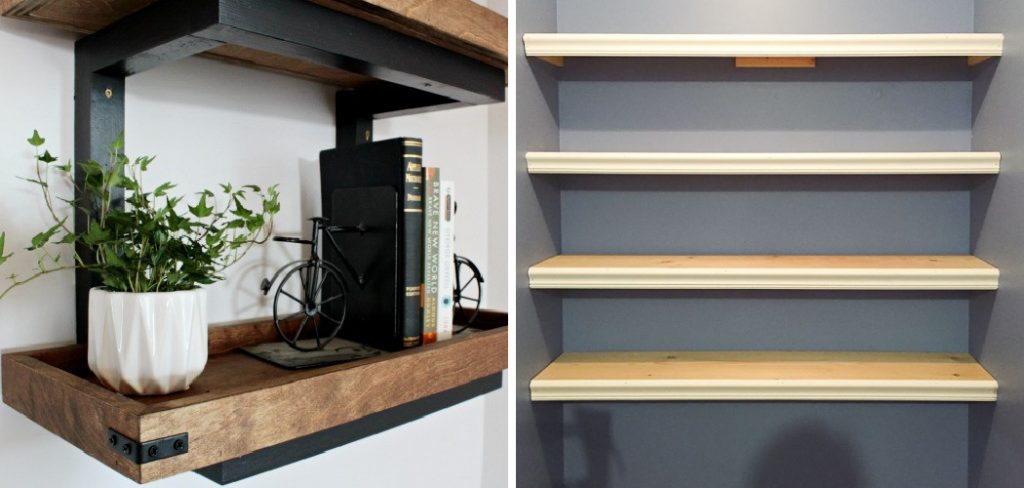
Wall shelves are a practical and stylish way to add storage and decoration to any room in your home. Whether you need a place to display books, showcase decorative items, or organize everyday essentials, building your wall shelves can be a rewarding and cost-effective project. With a little planning, some basic tools, and a dash of creativity, you can create custom shelves that perfectly suit your space and needs.
This guide on how to make wall shelves will walk you through the process step by step, making it easy for beginners and experienced DIYers alike.
What Are the Benefits of Building Your Own Wall Shelves?
There are many benefits to building your diy corner desk. Here are a few reasons why you should consider making your own instead of purchasing pre-made shelves:
- Customization: By building your wall shelves, you have complete control over the design, size, and materials used. This allows you to create shelves that fit perfectly in your space and match your style.
- Cost-effective: Making your wall shelves can be a much more affordable option than buying them from a store. You can save money by using materials you already have on hand or purchasing less expensive options at a hardware store.
- Personal Satisfaction: There’s something satisfying about creating something with your own hands and seeing it incorporated into your home. Making your own wall shelves gives you a sense of pride in your creation and a deeper connection to your living space.
- Versatile: Wall shelves can be used for various purposes, whether displaying decor, organizing books and knick-knacks, or even as storage for kitchen items. By making your own shelves, you can customize them for a specific purpose or change their usage as needed.
What Will You Need?
You will need a few essential materials and tools to make your own wall shelves. Here is a list of things you may need:
- Wooden Boards: Wooden boards are the most crucial material for making wall shelves. Depending on your budget and desired aesthetic, you can choose from various types of wood, such as pine, oak, or plywood.
- Saw: A saw is necessary to cut the wooden boards to the desired size and shape.
- Measuring Tape and Ruler: Accurate measurements are essential when building sturdy and functional shelves. A measuring tape and ruler will help ensure your shelves are precisely the size you want.
- Drill and Screws: A drill is necessary for creating holes in the wooden boards to attach them. Choose the appropriate size of screws depending on the thickness of your boards.
- Sandpaper: Sanding the edges and surfaces of your shelves will give them a smooth finish and prevent any splinters or rough patches.
- Wood Glue: While not always necessary, wood glue can provide additional support and stability for your shelves. It can also help fill in any gaps or imperfections in the wood.
8 Easy Steps on How to Make Wall Shelves
Step 1: Measure and Plan
Start by determining the space where you want to install your wall shelves. Use a measuring tape to accurately measure the area, including the height, width, and depth. Consider the purpose of your shelves—whether for books, decorative items, or storage—as this will influence their dimensions and weight capacity.
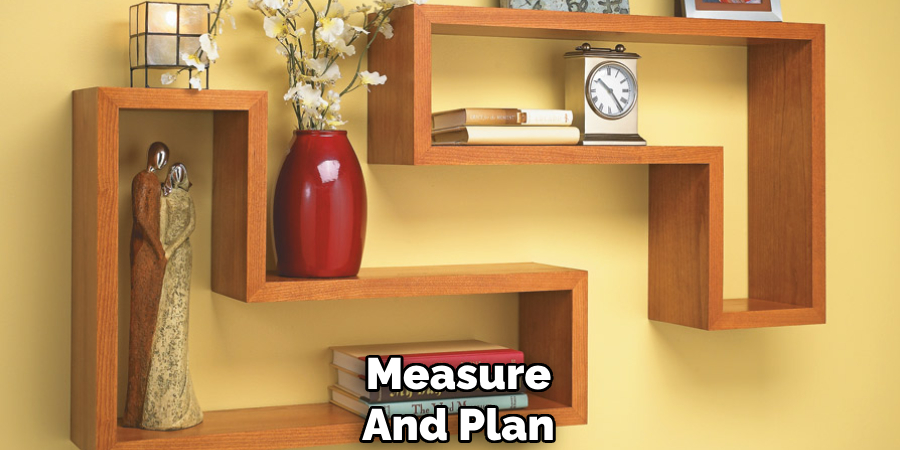
Make sure to account for the thickness of the boards and the brackets when planning your design. Sketch a rough diagram of the shelves, noting the placement and spacing. Proper planning at this stage will ensure that your shelves fit seamlessly into your desired location and meet your functional needs.
Step 2: Cutting the Boards
Using your measurements and design plan from Step 1, it’s time to cut the boards to the appropriate sizes. Select a high-quality wood or material that complements your space and meets your functional requirements. Before cutting, ensure your workspace is clean and safe, with the boards securely clamped to avoid movement. Use a measuring tape and a pencil to mark the exact dimensions, double-checking your measurements to prevent errors.
A circular or table saw is recommended for straight, precise cuts, while a hand saw can be used for smaller projects or those requiring intricate detailing. Always wear safety goggles and gloves to protect yourself during the cutting process. Sand down the edges of each cut board to remove roughness and splinters, ensuring a smooth finish that’s easier to work with in the next steps. Taking your time to cut accurately will make assembly much easier and give your shelves a polished, professional appearance.
Step 3: Assemble the Shelf Frame
Begin assembling the frame by securing the cut boards together. Use wood screws and a cordless drill to join the edges firmly, creating a sturdy structure. It’s helpful to use a square or clamps to ensure the corners are aligned perfectly at 90 degrees. Start with the sides and top boards, then attach the bottom board to complete the basic frame. Double-check all connections to confirm they are tight and secure, as this will provide strength and durability to your shelves.
Step 4: Sand and Prepare the Frame
Once the frame is assembled, use sandpaper or an electric sander to smooth rough edges or surfaces. Start with a coarse-grit sandpaper and gradually move to finer grits for a polished finish.
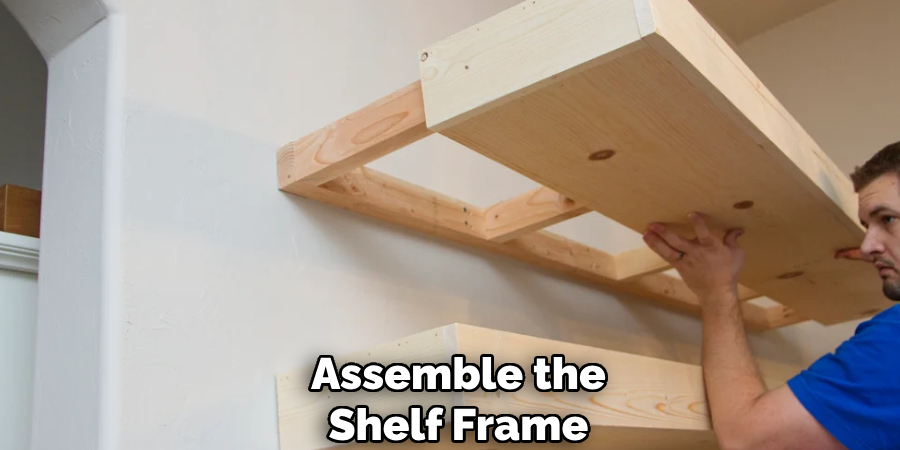
Pay special attention to the corners and joints to ensure they are even and safe to handle. Dust off the frame with a clean cloth or a vacuum to remove residual wood particles. At this stage, you can fill any visible gaps or holes with wood filler for an even surface, letting it dry fully before proceeding to the next step.
Step 5: Applying a Primer
Once the frame is sanded and cleaned, apply a coat of primer to prepare the wood for painting or staining. Choose a primer that is compatible with your chosen finish and use a brush or roller to apply it evenly across the surface. Cover all edges, corners, and hard-to-reach areas to ensure a uniform base. Allow the primer to dry completely as per the manufacturer’s instructions before moving on to the next step.
Step 6: Painting or Staining
Once the primer is dry, you are ready to apply your chosen finish. Whether you decide to paint or stain, make sure to use a high-quality product that is suitable for wood surfaces.
Use long, even strokes with a brush or roller to cover the entire frame, including edges and corners. Apply multiple coats if necessary, allowing each coat to dry completely before adding another layer.
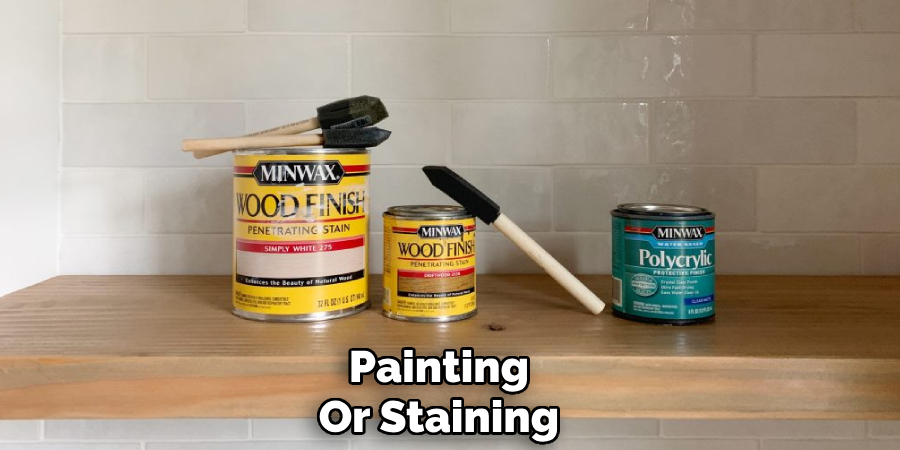
Step 7: Finishing Touches
After thoroughly drying the paint or stain, you can add finishing touches to your frame. This could include adding decorative elements such as trim or molding, or using a wood filler to smooth out any imperfections in the surface. You can apply a sealant or polyurethane coat for added durability and shine.
Step 8: Mounting and Displaying Your Finished Frame
Once your frame is thoroughly dried and all finishing touches have been completed, it is time to mount and display your work. Begin by carefully attaching any hardware needed for mounting, such as hooks, brackets, or a wire hanger, on the back of the frame. Ensure the hardware is securely fastened to prevent any accidents when the frame is displayed. If the frame is intended to be hung, consider using a level to ensure it sits straight on the wall. For added stability, use proper wall anchors or adhesive hooks based on the weight of the frame and the type of wall surface.
If your frame stands on a surface, such as a table or shelf, consider adding a stand or an easel backing for support. Always position the frame in a space that complements its design and enhances the room’s overall décor. Proper placement can significantly elevate the aesthetics of your artwork, photograph, or any display held within the frame. Once mounted, admire your handiwork and enjoy the personal touch it brings to your space.
By following these simple tips, you can create a beautiful and functional frame that will protect your artwork and enhance its beauty.
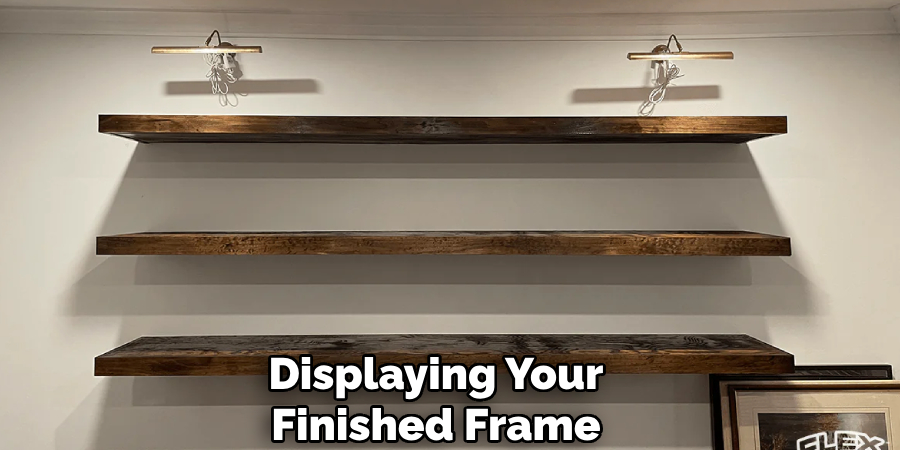
Conclusion
Creating wall shelves is a rewarding project that combines functionality and design. By carefully selecting materials, measuring your space accurately, and securely mounting the shelves, you can craft a storage solution that is both practical and visually appealing.
Whether you opt for a minimalist look or a more intricate design, wall shelves can enhance the organization and style of any room. With attention to detail and a bit of creativity, your custom shelves will serve a purpose and add a personal touch to your home décor.
Hopefully, the article on how to make wall shelves has given you some useful tips and inspiration to create your own unique storage solution. So why not give wall shelves a try and see how they can transform your space? Happy crafting!
Huston Douthit is a distinguished figure in the world of furniture design, with a decade of expertise creating innovative and sustainable furniture solutions. His professional focus lies in merging traditional craftsmanship with modern manufacturing techniques, fostering designs that are both practical and environmentally conscious. As the author of Fruniturix, Huston delves into the art and science of furniture-making, inspiring artisans and industry professionals alike.
Education
- RMIT University (Melbourne, Australia)
Associate Degree in Design (Furniture)- Focus on sustainable design, industry-driven projects, and practical craftsmanship.
- Gained hands-on experience with traditional and digital manufacturing tools, such as CAD and CNC software.
- Nottingham Trent University (United Kingdom)
Bachelor’s in Furniture and Product Design (Honors)- Specialized in product design with a focus on blending creativity with production techniques.
- Participated in industry projects, working with companies like John Lewis and Vitsoe to gain real-world insights.
Publications and Impact
In Fruniturix, Huston shares his insights on furniture design processes, materials, and strategies for efficient production. His writing bridges the gap between artisan knowledge and modern industry needs, making it a must-read for both budding designers and seasoned professionals.